Understanding Electrical Plastic Molding
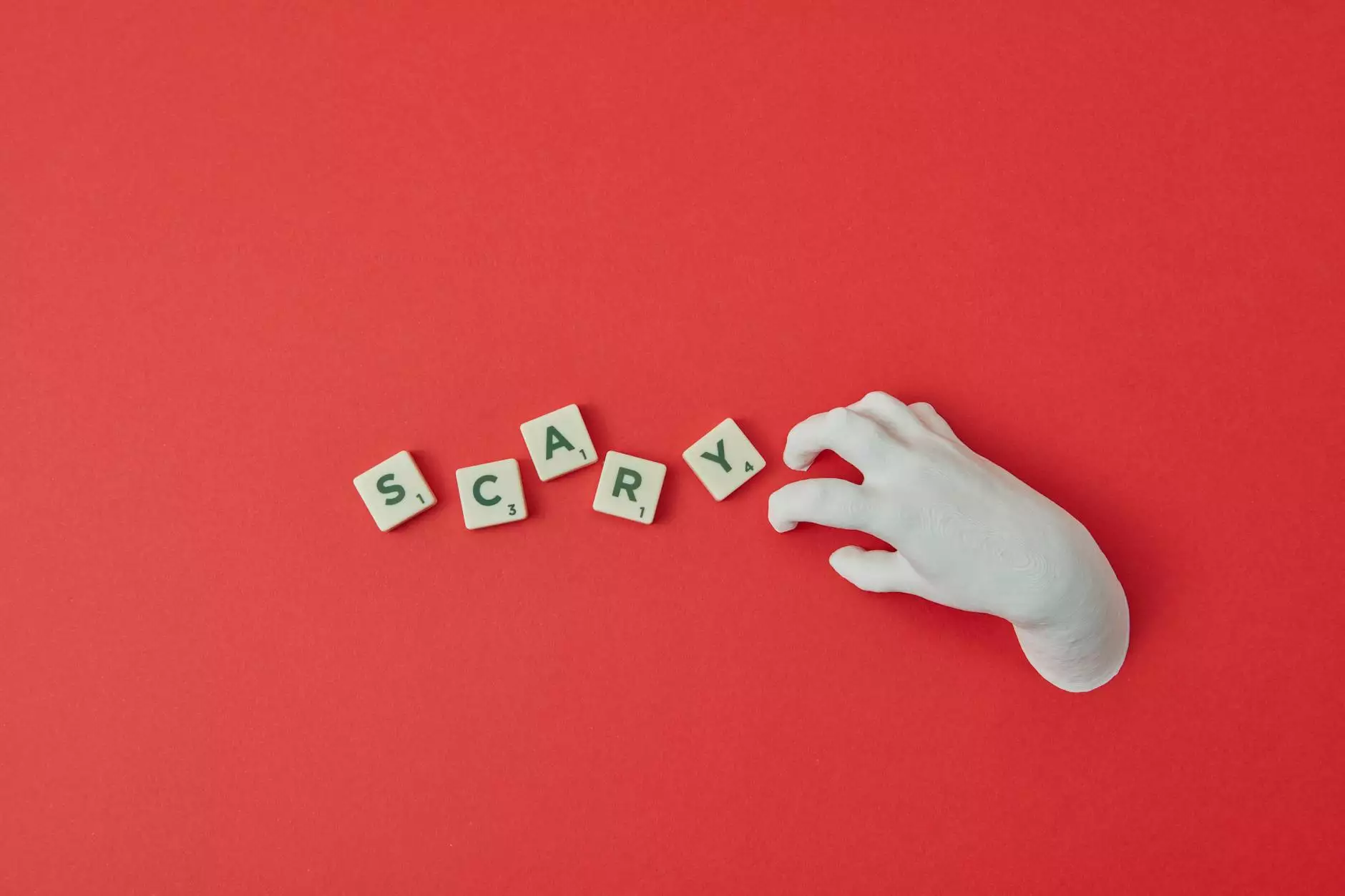
Electrical plastic molding is an essential process in the modern manufacturing landscape, particularly within the metal fabrication industry. This technique allows for the creation of intricate plastic components that are not only versatile but also durable, making them ideal for various applications. This article aims to delve deep into the world of electrical plastic molding, exploring its significance, techniques, benefits, and its undeniable impact on businesses within the metal fabrication domain.
What is Electrical Plastic Molding?
Electrical plastic molding is a manufacturing process that involves shaping heated plastic materials into a specific mold. This process is widely used for producing various components used in electrical devices and consumer products. The molding technique typically involves:
- Heating the plastic until it becomes malleable.
- Injecting the heated plastic into a mold.
- Cooling the mold to solidify the plastic into the desired shape.
- Removing the finished product from the mold.
This method not only shapes plastic into precise forms but also allows for the incorporation of various materials to enhance functionality, such as metal components or additives that improve strength and durability.
Key Techniques in Electrical Plastic Molding
The electrical plastic molding process encompasses various techniques that cater to different manufacturing needs. Understanding these methods aids businesses in selecting the right process for their specific applications. Some of the most common techniques include:
1. Injection Molding
This is the most widely used method for electrical plastic molding. The process involves injecting molten plastic into a mold cavity under high pressure. This technique is celebrated for its ability to produce large volumes of uniform products with precision.
2. Blow Molding
Blow molding is primarily employed for creating hollow plastic parts. In this method, a tube of molten plastic (parison) is inflated to fill a mold cavity. This technique is widely used in manufacturing plastic bottles and containers but has also found applications in producing parts for electrical devices.
3. Compression Molding
This method involves placing a pre-measured amount of plastic into a heated mold. The mold is then closed, and heat and pressure cause the plastic to flow and take the shape of the mold. Compression molding is often used for larger parts where high precision is not as critical.
4. Thermoforming
Thermoforming involves heating a plastic sheet until it becomes pliable and then forming it over a mold. This technique is less precise than injection molding but is ideal for producing larger components at a lower cost.
The Advantages of Electrical Plastic Molding
Businesses that utilize electrical plastic molding can reap numerous benefits, including:
- Cost-Effectiveness: Once the initial mold is created, producing each component is relatively inexpensive, particularly at scale.
- Versatility: Different plastic materials can be used to achieve a variety of properties, such as heat resistance, flexibility, and strength.
- Precision: Molding techniques can produce highly precise and complex shapes that are consistent across multiple productions.
- Reduced Waste: Since the excess plastic can often be recycled or reused, this process is more sustainable compared to traditional manufacturing methods.
- Speed: The molding process can be executed quickly, allowing for rapid production timelines, critical for meeting market demands.
Applications of Electrical Plastic Molding in Metal Fabrication
Within the realm of metal fabrication, electrical plastic molding has numerous applications, including:
- Electrical Enclosures: Custom plastic enclosures are essential for protecting sensitive electrical components from environmental factors.
- Connectors and Insulators: Plastic molded parts serve as essential connectors and insulators in various electrical applications, ensuring safety and functionality.
- Components for Appliances: Many electrical appliances rely on molded plastic parts, from housings to internal components.
- Automotive Parts: The automotive industry uses molded parts in various applications, from dashboard components to wiring housings.
The Role of Quality Control in Electrical Plastic Molding
To ensure that the electrical plastic molding process yields high-quality products, implementing stringent quality control measures is vital. This involves:
- Material Inspection: Verifying that the plastic materials meet the necessary standards for durability and performance.
- Mold Maintenance: Regularly checking and maintaining molds to prevent defects caused by wear and tear.
- Testing Finished Products: Conducting various tests such as dimensional checks, impact resistance tests, and electrical safety tests to ensure compliance with industry standards.
Challenges in Electrical Plastic Molding
While electrical plastic molding offers many benefits, it is not without challenges. Businesses must navigate issues such as:
- Mold Design Complexity: Designing molds can be complex and costly, particularly for intricate components.
- Material Selection: Choosing the right plastic material is crucial; selecting a substandard material can lead to failures in performance.
- Production Speed Versus Quality: Balancing rapid production rates with quality can be challenging, particularly under tight deadlines.
Emerging Trends in Electrical Plastic Molding
The field of electrical plastic molding is constantly evolving. Some emerging trends that could shape the future of this industry include:
- Increased Use of Sustainable Materials: Manufacturers are increasingly turning to biodegradable and recycled plastics, aligning with global sustainability goals.
- Advancements in 3D Printing: The integration of 3D printing technologies in the molding process allows for faster and more innovative designs.
- Smart Materials: Research into smart materials that can change properties based on environmental factors is opening new avenues for production.
Conclusion: Harnessing the Power of Electrical Plastic Molding
As we have seen, electrical plastic molding plays a pivotal role in the metal fabrication industry. With its myriad advantages, such as cost-effectiveness, precision, and versatility, it is a cornerstone of modern manufacturing. Businesses that prioritize quality control and stay ahead of emerging trends will not only enhance their productivity but also cement their standing in a competitive marketplace.
For metal fabricators looking to leverage the benefits of electrical plastic molding, connecting with reliable partners like Deep Mould can provide invaluable insights and technological support. By investing in top-notch molding processes, materials, and training, your business can excel in producing high-quality products that meet and exceed market expectations.