Mastering Tool and Die Casting: A Comprehensive Guide for Metal Fabricators
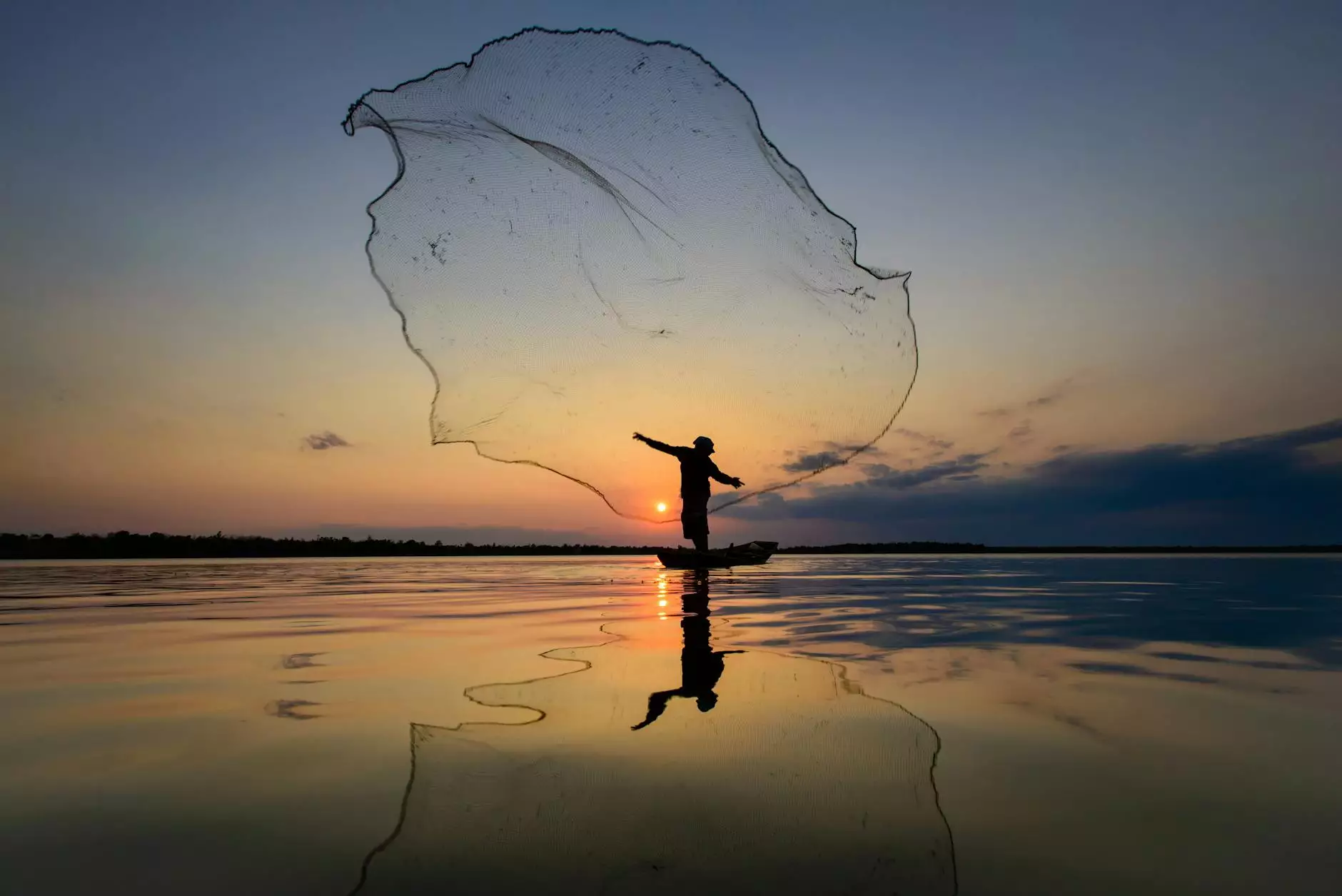
Tool and die casting is a pivotal process in the realm of metal fabrication, playing an essential role in producing intricate and high-quality components. This article delves deep into the significance of tool and die casting, the methodologies involved, and its benefits for contemporary businesses such as DeepMould.net. Whether you're a manufacturer, engineer, or simply someone interested in the metalworking industry, this guide is tailored to provide you with the insights you need.
Understanding Tool and Die Casting
At its core, tool and die casting is a manufacturing process that involves creating molds or dies into which molten metal is poured. This method allows for the precise shaping of metal components, enabling efficiency and scalability in production. Tooling, which comprises the design and creation of the molds, is crucial for achieving the desired specifications and tolerances.
The Process of Tool and Die Casting
The tool and die casting process can be broken down into several key steps:
- Design and Engineering: The initial stage involves the design of the component and the tooling required. Engineers utilize advanced 3D modeling software to create precise designs.
- Tooling Production: Once the designs are finalized, the molds are fabricated. This can involve various techniques including CNC machining and EDM (Electrical Discharge Machining).
- Melting and Pouring: The selected metal is heated to its melting point and poured into the molds. Common metals used include aluminum, zinc, and magnesium.
- Cooling and Solidification: The molten metal cools and solidifies within the die, taking on its shape.
- Demolding: After cooling, the component is removed from the mold, often requiring additional steps for finishing.
- Finishing and Quality Control: Finally, the completed parts undergo various finishing processes and stringent quality checks to ensure they meet the required specifications.
Applications of Tool and Die Casting
The versatility of tool and die casting enables its application across various industries. Here are some notable areas where this process is utilized:
- Aerospace: Manufacturing lightweight and complex components for aircraft and spacecraft.
- Automotive: Production of engine components and parts that require high durability and precision.
- Electronics: Enclosures and heat sinks that need to dissipate heat effectively.
- Consumer Goods: Items such as household appliances and furnishings that require aesthetic appeal along with functionality.
Benefits of Tool and Die Casting
The adoption of tool and die casting offers numerous advantages, making it a preferred choice among metal fabricators:
1. Precision and Consistency
By utilizing high-quality molds, manufacturers can produce parts that are consistent in size and detail. This precision is vital in industries where tolerances are critical.
2. Improved Production Efficiency
Once a mold is created, the production of parts can be done rapidly, significantly decreasing turnaround times compared to other methods such as machining.
3. Material Savings
Tool and die casting often requires less material than traditional machining, as the excess material in machining is a byproduct rather than an integral part of the process. This results in greater resource efficiency and lower costs.
4. Complex Geometries
This casting method allows for the creation of intricate shapes and designs that might be impossible or economically unfeasible with other fabrication techniques.
5. Surface Finish
Parts produced via die casting have superior surface finishes and can often require little to no machining after the casting process, further saving time and cost.
Challenges in Tool and Die Casting
While tool and die casting presents many advantages, it is also crucial to be aware of its challenges:
1. Upfront Costs
The initial investment in creating molds and tooling can be significant, potentially hindering smaller businesses from entering this market.
2. Limited Material Options
Not all metals are suitable for tool and die casting. The range of materials is primarily limited to non-ferrous metals, which can restrict options in some applications.
3. Risk of Defects
If not properly managed, issues such as air pockets, misalignment of molds, or overheating can result in defects in the final product, necessitating strict quality controls.
Future Trends in Tool and Die Casting
The landscape of tool and die casting is set to evolve with advancements in technology and changing manufacturing demands. Here are some trends to watch:
1. Automation and Smart Technologies
The integration of Industry 4.0 technologies, such as IoT (Internet of Things) and AI (Artificial Intelligence), is streamlining the casting process, enhancing efficiency and reducing human error.
2. Sustainable Practices
As industries lean towards sustainability, the adoption of eco-friendly metals and recycling of materials post-production will become increasingly prevalent, ensuring minimal waste.
3. Additive Manufacturing
3D printing technologies are influencing die design, allowing for rapid prototyping and alterations without significant downtime.
The Role of DeepMould in Tool and Die Casting
As a leader in the field, DeepMould.net is committed to providing its clients with innovative solutions in tool and die casting. Our experienced team harnesses the latest technologies and methods to enhance quality and efficiency, ensuring we meet the needs of our diverse customer base. Our dedication to excellence makes us a go-to partner for businesses in various sectors, from automotive to aerospace.
Why Choose DeepMould.net?
Here are some key reasons to consider DeepMould for your next project:
- Expertise: Extensive industry experience with a focus on precision and quality.
- State-of-the-Art Equipment: Utilization of advanced machinery and technology for optimal results.
- Competitive Pricing: Offering cost-effective solutions without compromising on quality.
- Custom Solutions: Tailored services to meet the specific needs of clients across different industries.
- Commitment to Sustainability: Efforts to minimize environmental impact through eco-friendly practices.
Conclusion
In conclusion, tool and die casting stands as a superior metal fabrication method, combining precision, efficiency, and versatility. By understanding its processes, applications, benefits, and the emerging trends, businesses can leverage this technique to enhance their productivity and product quality. With partners like DeepMould.net, companies can confidently navigate the complexities of metalworking and achieve their manufacturing goals.
For more information on how our services can benefit your organization, feel free to reach out to us at DeepMould.net.