LEVe Inspection in South Wales: A Comprehensive Guide
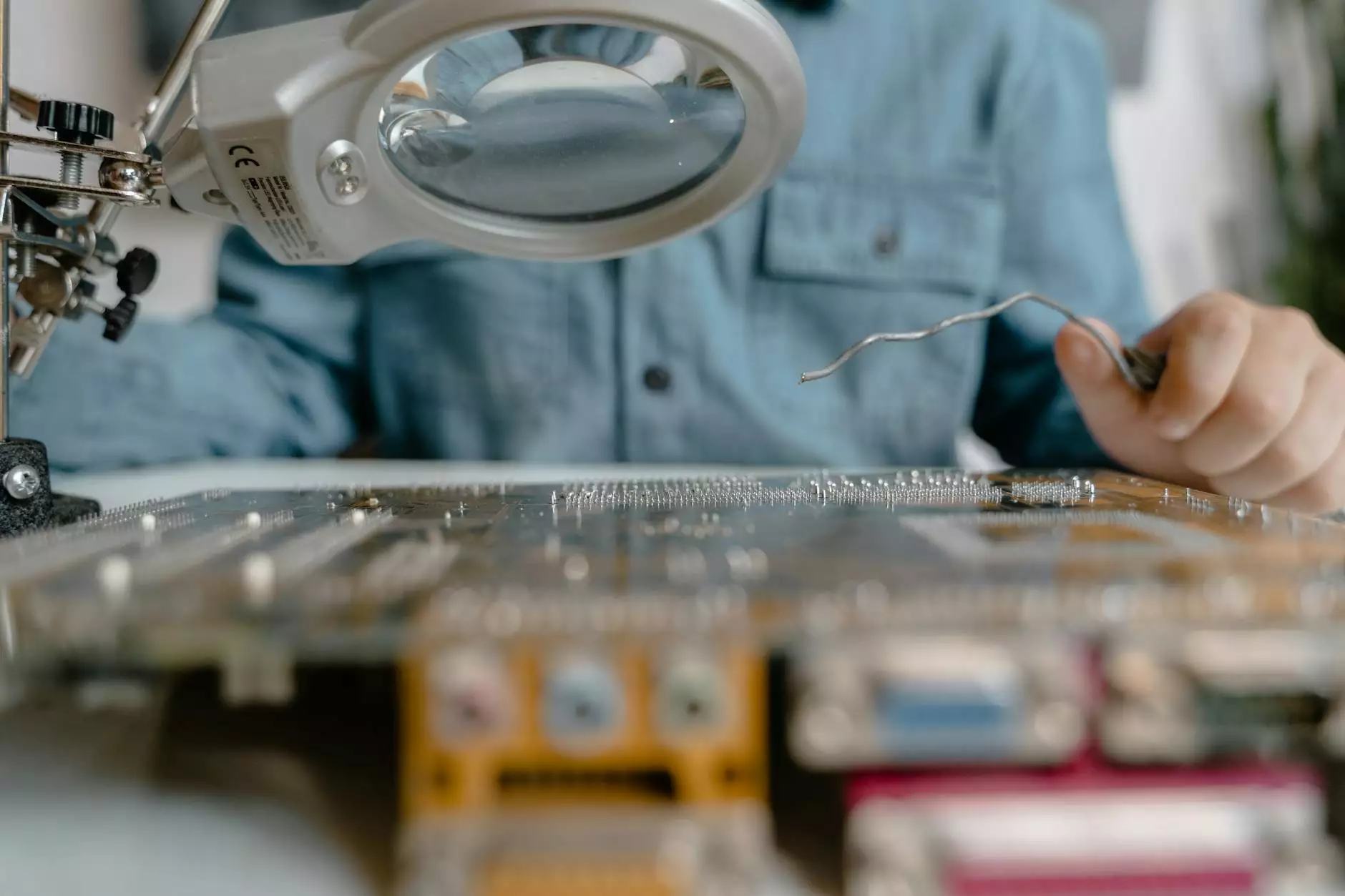
The importance of LEVe inspection South Wales cannot be overstated. In today's industrial landscape, businesses must prioritize safety and compliance to protect their employees and maintain operational standards. This article delves into the intricacies of LEV (Local Exhaust Ventilation) inspections, emphasizing their benefits, the legal framework surrounding them, and why they are crucial for businesses operating in South Wales.
What is LEV?
Local Exhaust Ventilation (LEV) systems are engineering controls designed to capture and remove airborne contaminants generated during various workplace processes. These can include dust, fumes, vapors, and mists that can pose health risks to employees. Understanding LEV systems and their inspections is vital for any business aiming to create a safe work environment.
The Importance of LEV Systems
- Health Protection: LEV systems play a crucial role in safeguarding employees from harmful substances.
- Regulatory Compliance: Regular inspections ensure businesses meet health and safety regulations.
- Improved Work Environment: A clean and safe working space enhances productivity and morale among employees.
- Risk Management: Properly functioning LEV systems reduce the risk of accidents and health-related issues.
Legal Framework for LEV Inspection in South Wales
In South Wales, as in the rest of the UK, businesses are legally required to maintain safe working conditions. The Health and Safety at Work Act 1974 mandates employers to protect the health and safety of their employees. Coupled with the Control of Substances Hazardous to Health (COSHH) Regulations 2002, these laws necessitate regular LEV inspections to ensure that systems are functioning effectively and controlling exposure to hazardous substances.
Key Legal Requirements
- Frequency of Inspections: LEV systems must be tested at least every 14 months, as per HSE guidance.
- Competence of Inspectors: Inspections should be conducted by competent persons with appropriate training and experience.
- Documentation: Detailed records of inspections and maintenance tasks must be kept for compliance purposes.
The LEV Inspection Process
Conducting a LEV inspection in South Wales involves several steps to ensure that the ventilation systems are working correctly. Here’s an in-depth look at the process undertaken during inspections:
1. Pre-Inspection Preparation
Before the inspection, it’s important to gather relevant documents and data pertaining to the LEV system. This includes:
- Previous inspection reports
- Service records
- System specifications
- Risk assessments related to hazardous substances
2. Visual Inspection
The inspector will conduct a thorough visual examination of the LEV system. This includes checking:
- The overall condition of the equipment
- The integrity of ductwork and connections
- The function of fans and filters
- Signs of contamination or wear
3. Performance Testing
To ensure effective operation, performance testing is conducted. This may involve:
- Measuring airflow rates
- Assessing the capture velocity at the point of emission
- Testing filter efficiency
4. Reporting and Recommendations
Following the inspection, a comprehensive report is generated. This report includes:
- A summary of findings
- Compliance status with legislation
- Recommendations for repairs, maintenance, or improvements
Benefits of Regular LEV Inspections
Investing in regular LEV inspections brings numerous advantages to businesses, particularly in South Wales. Here are the main benefits:
1. Enhanced Employee Safety
Regular inspections help identify and mitigate potential hazards that could jeopardize employee health. A safe workspace fosters a culture of safety, leading to higher employee satisfaction and retention.
2. Reduced Risk of Legal Action
By ensuring compliance with health and safety regulations, businesses can significantly reduce their risk of legal action. Non-compliance can lead to severe penalties and fines.
3. Improved Operational Efficiency
Well-maintained LEV systems improve general operational efficiency. By removing contaminants effectively, these systems ensure that workers can perform their tasks without distractions or health concerns.
4. Cost Savings
While there are costs associated with inspections and maintenance, the long-term savings from avoided fines, reduced employee health claims, and improved productivity outweigh these expenses.
Finding the Right LEV Inspection Service in South Wales
Choosing a competent service provider for LEV inspection in South Wales is crucial. When searching for the right company, consider the following factors:
1. Experience and Qualifications
Ensure the company has relevant experience in LEV systems and certified inspectors knowledgeable about legal requirements.
2. Reputation and Reviews
Look for testimonials and reviews from previous clients to gauge the reliability and quality of service offered.
3. Range of Services
Opt for a provider that offers comprehensive services, including installation, maintenance, and emergency repairs, in addition to inspections.
4. Transparency in Pricing
Request detailed quotes and ensure that there are no hidden charges associated with the inspection process.
Conclusion
In conclusion, understanding the significance of LEV inspection South Wales is imperative for any business committed to safety and compliance. Regular inspections not only protect employees but also ensure that businesses meet legal standards, ultimately driving operational success. By prioritizing the health and safety of your workforce through effective LEV systems, companies can cultivate a positive work environment that supports productivity and growth.
For more information on LEV inspections and to ensure your business meets all health and safety requirements, consider reaching out to reliable resources such as Safe Plant UK. They provide expert guidance tailored specifically to the needs of businesses in South Wales and beyond.